Special Solutions from the Specialist: A Cooled Material Flow from the Material Supply to the Tablet
The major challenge of our project was the melting temperature of the compression powder of Tmelt ≈ 6 °C, which required a maximum die table temperature of Tdie table max = 5 °C. The initial in-vestigations confirmed that the solutions available to date were, as already suspected, insufficient to reach the required temperature.
When investigating how the temperature of the compressed material flow behaved along the tablet-ing process - from material feed to tablet discharge - it became clear that the customer's require-ments could only be achieved with a comprehensive cooling strategy. The temperature of the die table Tdie table played a decisive role here, as it there is inherent heat transfer to the die tablet during the compression process.
Constant cooling along the tableting process was ultimately achieved by the following material flow sequence:
- Temperature control of the production room to Troom = 15 °C ± 1 °C at 50 % ± 5 % humidity.
- Provision of the compression material with Tpowder = 4 °C ± 1 °C.
- Provision of a cooling fluid with Tcooling medium = 2 °C ± 0.5 °C including reprocessing.
- The cooling fluid flows through the material feed, the clamping plate and the turret (including the die table) via separate cooling circuits.
- The material feed is adapted with an insulated cooling jacket that achieves a temperature of Tfeed < 4 °C.
- The insulated feeder clamping plate (Figure 1) equipped with "cooling channels" is cooled to
- Tclamping plate < 4 °C by means of the cooling fluid. In addition, a cooling plate is mounted on the feeder cover.
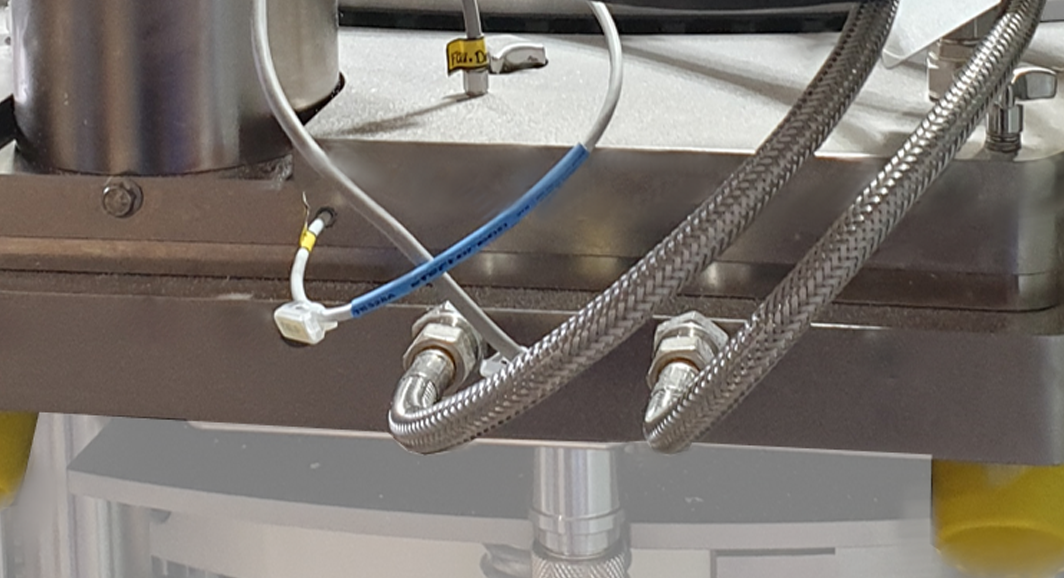
The turret is also equipped with "cooling channels". The cooling fluid enters the inner area via a swivel joint and is directed through the upper part of the turret to the die table.
There, the cooling fluid is guided around the dies (up to the edge of the die table (Figure 2), further into the lower part of the turret and finally pumped out of the inner area into the reservoir.
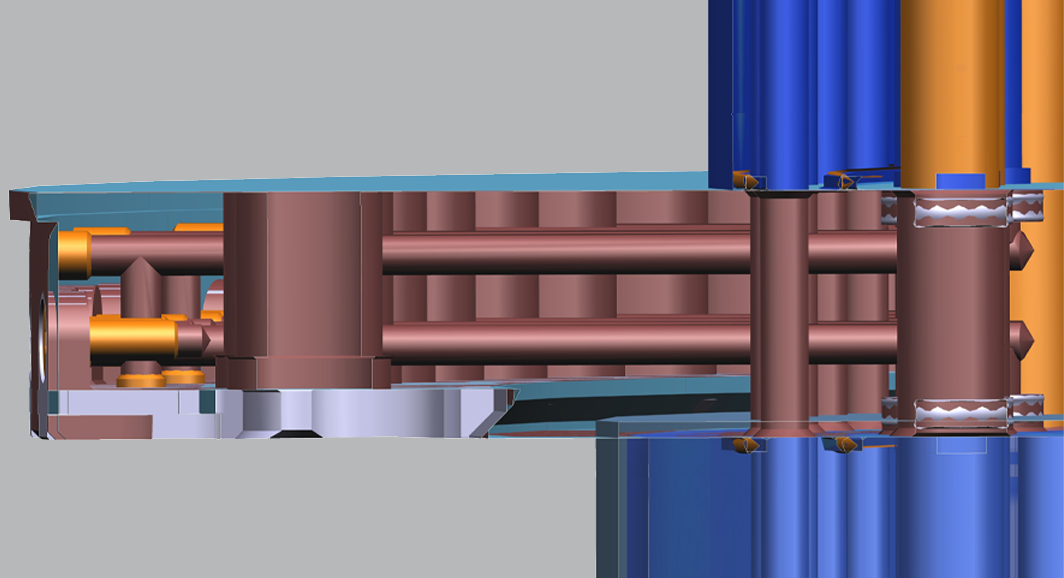
In order to keep the experimental effort as low as possible, we carried out a CFD flow and tempera-ture analysis of the turret cooling with iterative improvements. The result of these simulations was a design solution that provided a die table temperature of Tdie table < 4 °C (Figure 3).
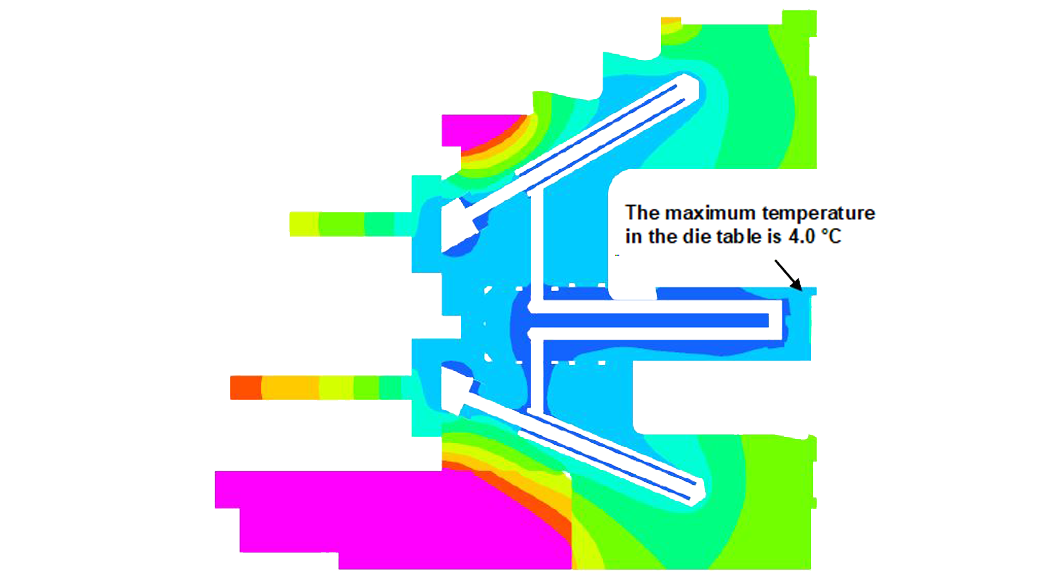
Even the outside of the die table had this low temperature (Figure 4).
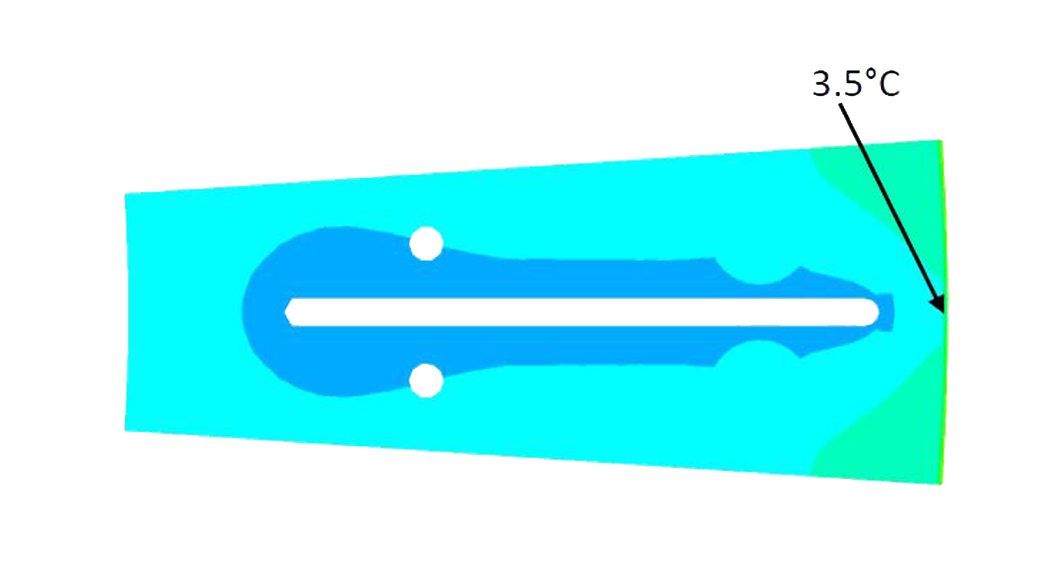
The next step was to implement and test a prototype. According to the simulation results, the ma-chine was operated for t = 10 minutes without compression material in order to set the steady-state temperature of the die table to Tdie table < 4 °C. Only at this point, the compression material was in-troduced to the press.
During the investigations, we were able to confirm with our test results that the temperature along the entire material flow was Tmaterial flow < 5 °C. During the measurements, which we carried out with thermocouples at representative points of the material flow described above, we detected neither condensation in the compression zone nor melting of the compression material. In addition, the tab-lets produced met the requirements of European Pharmacopeia 2.9.5.
We have thus not only confirmed the function of our design solution, but also solved the challenge of Tdie table max = 5 °C.
The development presented here is the premium version of a cooling concept that can be individually adapted to customer requirements - from punch tip cooling to cooled turrets and comprehen-sive cooling concepts. KORSCH AG thus offers all customers a perfectly customized solution when there is a need to address heat during the compression process.