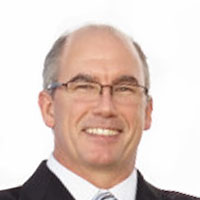
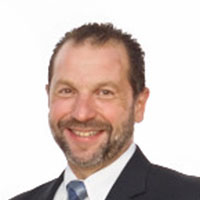
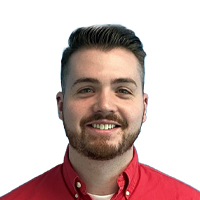
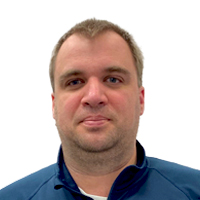
CUSTOMER CARE
We Care About Everything Around Your Tableting Process! Energize it!
KORSCH offers a global service capability that addresses all facets of tablet production support and optimization.
Our team of experienced experts provides far more than equipment repair and spare parts.
We work to understand your process and provide instructions and best practices to permit our customers to leverage our technology and to
realize the highest levels of product quality, equipment reliability, and production efficiency.
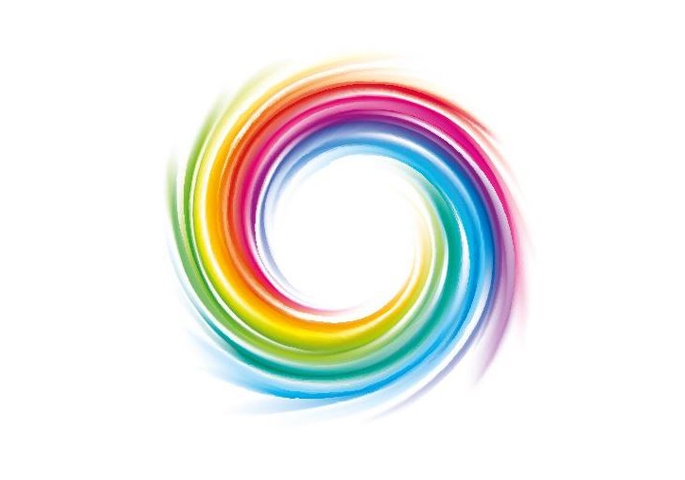
On-Site Support Services
What we offer:
- Qualification and validation
- Calibration services
- Training certification
- Preventative maintenance
- Process optimization
- Service agreements
- Peripheral equipment integration
- Remote support
Qualification, Validation & Calibration
Executed by KORSCH Experts
KORSCH offers a comprehensive validation documentation capability. Our professional documentation group works closely with our engineering and project management team to deliver a package of specification documents, validation protocols, and support documents to fully meet the project requirements. The qualification protocols are executed on-site by our service experts to fully document the safety and functionality of the system.
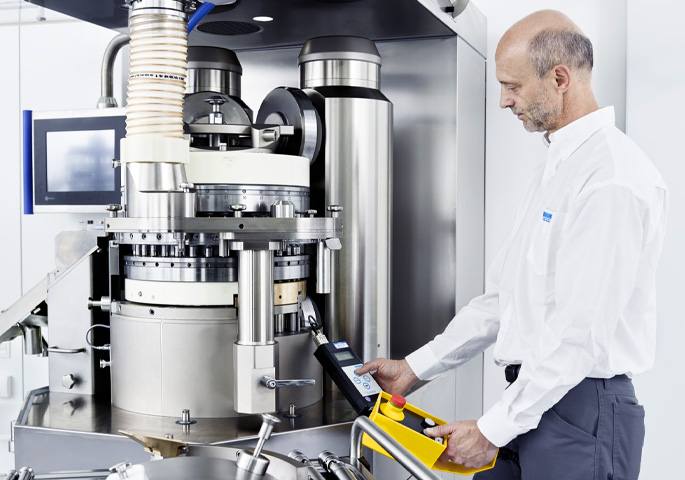
Calibration
Executed by KORSCH Experts.
KORSCH provides complete calibration services for all instrumentation on the tablet press, including rotational speed, linear punch position, and press forces. The Calibration Qualification document includes the calibration test method, required accuracy, and acceptance criteria.
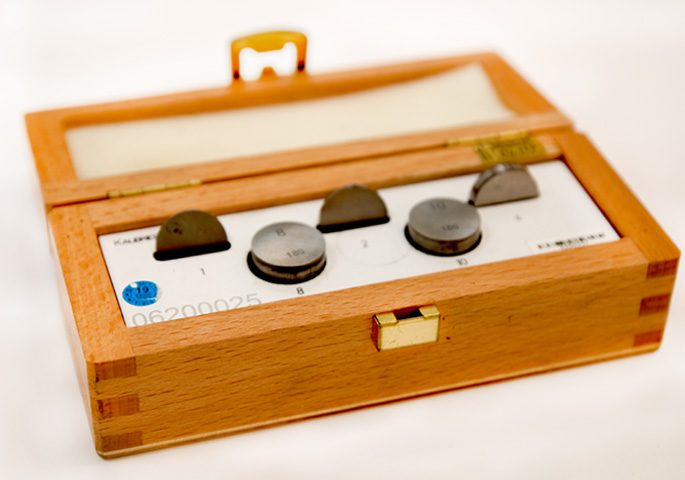
CALIBRATION PACKAGE INCLUDES
- Strain gauge verification
- Rotational speed verification
- Linear punch positions
- Calibration using certified standards
- Calibration certification
Service Agreements
For Continued Reliability
KORSCH offers a wide variety of service contracts that are designed to ensure the optimal performance of your KORSCH machine. Each service contract is customized to meet the specific requirements of the customer and the application. Service contracts permit a predictable, fixed price approach to annual maintenance and service of your KORSCH machine.
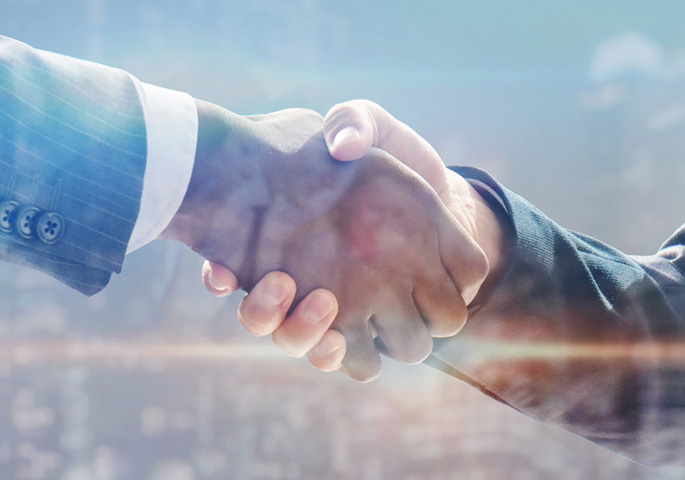
Service Contract Components
- Equipment calibration
- Preventative maintenance inspection
- Operation and maintenance training
- Process optimization support
- Spare part and wear part packages
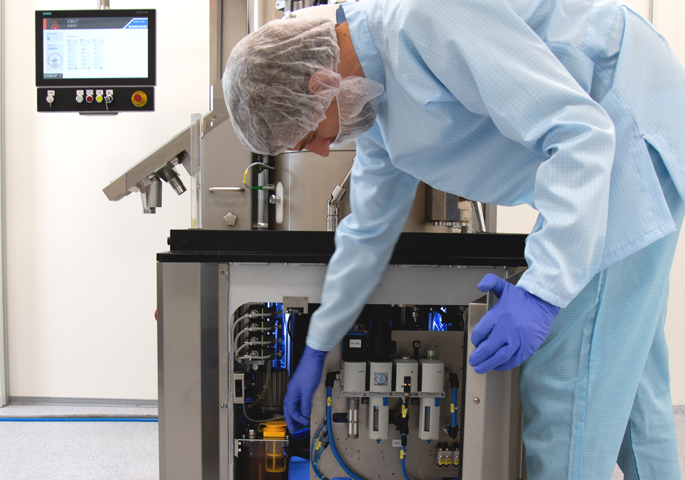
PREVENTATIVE MAINTENANCE
Scheduled and Predictable
To ensure optimal machine performance and uptime, KORSCH offers a comprehensive Preventative Maintenance Program which includes a detailed inspection of the key mechanical and control system components. A detailed PM protocol is utilized to assess the machine condition and a corresponding PM report is issued. The proactive implementation of the PM service will avoid unplanned downtime and ensure long term reliability.
Training Certification
Learn from Experts
Optimal performance requires a high level of operational competence. KORSCH on-site training will help your operators understand the machines and their control system, how to carry out maintenance tasks, and how to create recipes. Depending on the level of knowledge, the training can be implemented in the form of training courses or supervision.
For all courses, formal training certification is provided.
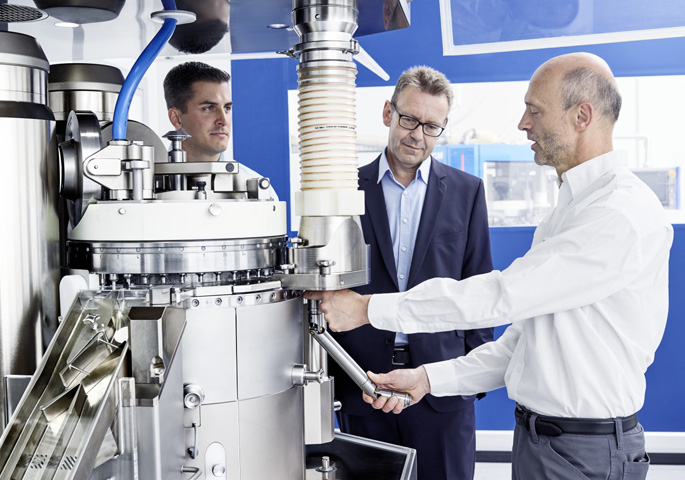
Training drives efficiency
Classroom and hands-on training provided by KORSCH helps users to achieve this optimum efficiency. Whether a machine operates at optimum efficiency depends on the proper setup and maintaining the machine in good working order. Therefore, it is critical to have well-trained operators and a skilled maintenance staff.
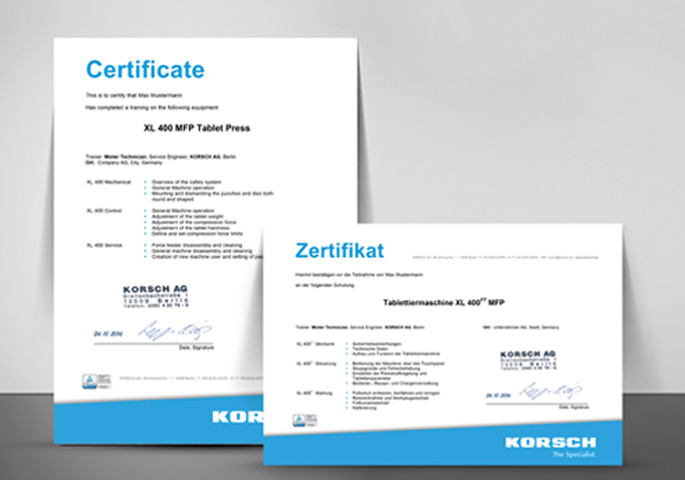
COMPREHENSIVE COURSE SELECTION
- Basic concepts of tablet compression
- Basic set-up and operation
- Advanced tablet press set-up and operation
- HMI administration
- Tablet press maintenance
- Tablet press calibration
- Tablet press trouble shooting
- Multi-layer technology
- Wash-in-place and high-containment technology
- PharmaResearch data acquisition
Remote Support
Cost Effective and Timely
All KORSCH machines have the capability to be supported remotely by experts at KORSCH. The result is expedited diagnostic support and minimal downtime. The remote session must be authorized and enabled at the customer site to ensure absolute security.
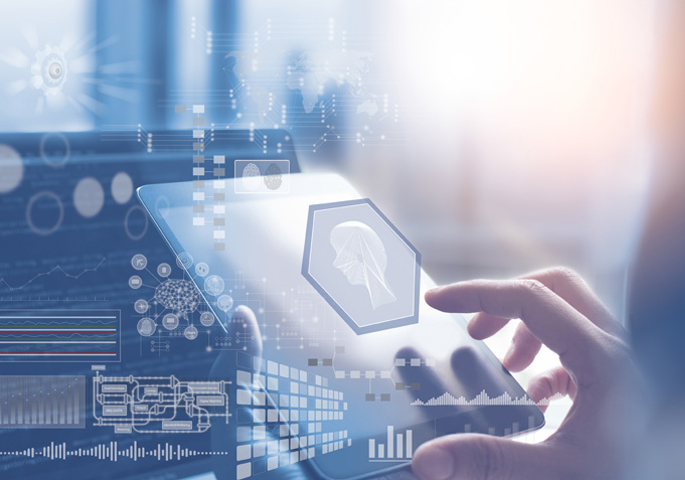
remote access capability permits
- Immediate fault diagnosis and support
- Analysis of PLC software
- Analysis of HMI software
- Analysis of drive parameters
- General system troubleshooting
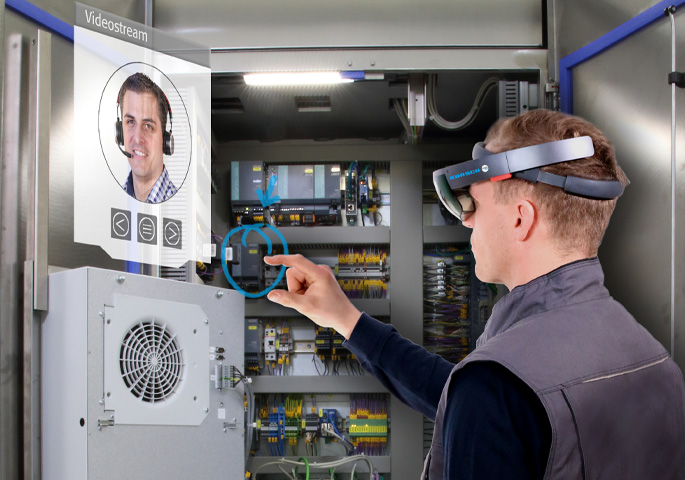
PharmaView®
Smart Holographic Operator Support
KORSCH brings data to life with advanced HoloLens technology to enhance the service experience and redefine the concept of technical support. The KORSCH PharmaView® enables a service setting which is augmented by digital content, technical holograms, and real-time expert support.
OEM SPARE PARTS SUPPORT
Peak operating performance can only be guaranteed with KORSCH OEM replacement parts, which are manufactured to exacting standards and tolerances, and with optimal materials. KORSCH OEM parts ensure reliable and long term operation, and protect your investment in KORSCH technology.
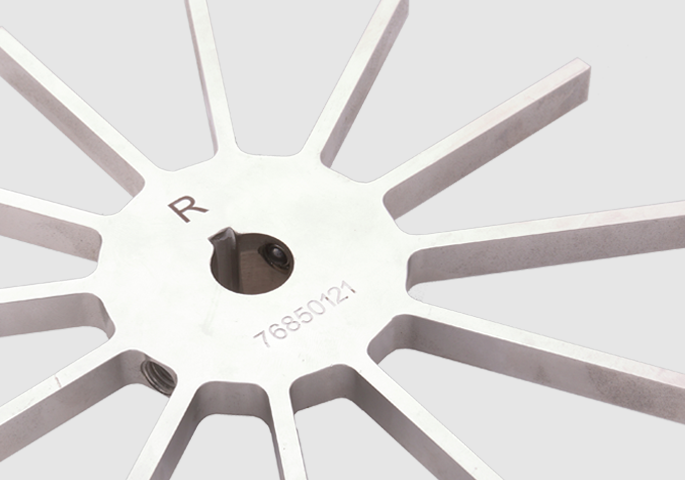
KORSCH SPARE PARTS
We offer a full range of OEM spare parts for all machine models, including mechanical, electrical and electronic components. Critical wear and spare parts are available for immediate delivery.

Your Benefits
- Quality, OEM spare parts with immediate availability
- Superior performance to optimize machine operation
- Technical support for spare part identification
- Access to all design enhancements and technical improvements
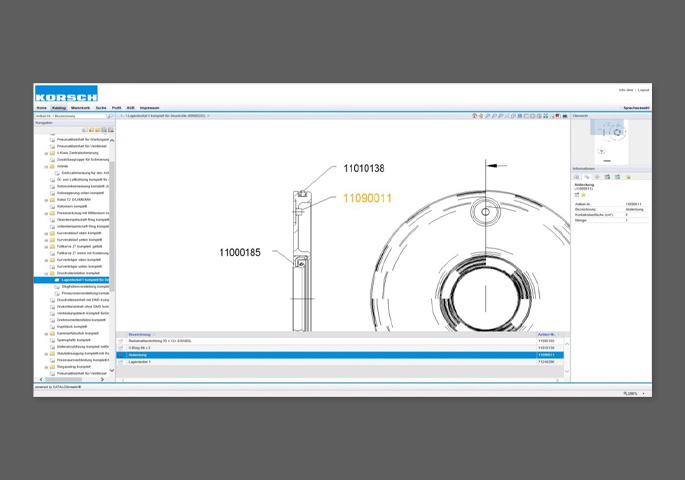
E-DOC
The Electronic Spare Parts Catalog features an intuitive and user-friendly interface to assist you in the procurement Process. Your benefits are:
- Simple navigation to find the right machine part quickly and easily
- Spare part list is linked to the drawings
- Wiring diagrams available on the same platform
- Easy ordering Process