DryCon® & WipCon® - KORSCH Containment
Containment
A Job for Specialists
Containment denotes a conceptual strategy for the safe handling of highly potent products during development, scale-up, and high-speed production. KORSCH containment tablet presses are designed in a GMP-compliant manner to ensure operator safety during all phases of setup, operation, and cleaning.
KORSCH Containment Categories
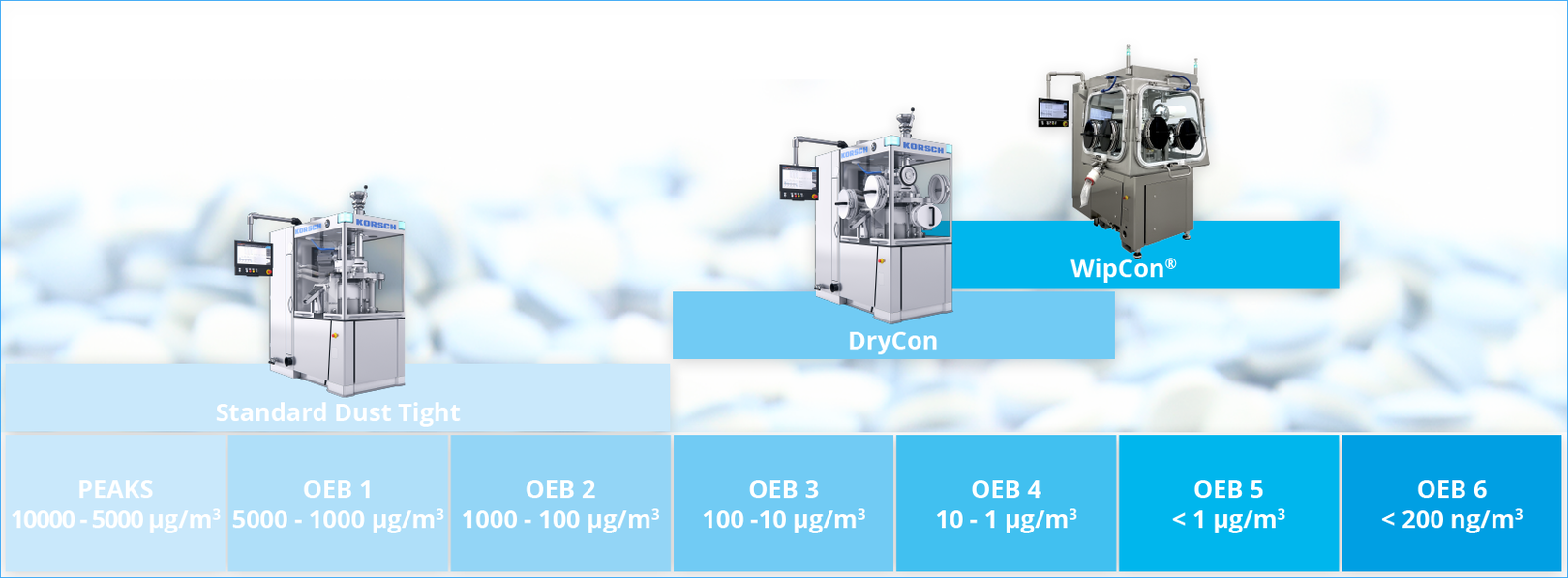
DryCon® Execution
The dry containment kit (DryCon®) on KORSCH presses permits a containment level of OEB 3 or OEB 4. The core of the DryCon® system is the Restricted Access Barrier System (RABS), which uses negative pressure control in the compression zone combined with window locks as well as a reinforcement of the dust tightness on the make/break connections. For all dry containment applications, cleaning is performed wearing personal protective equipment (PPE).
Enhancing the DryCon® Execution
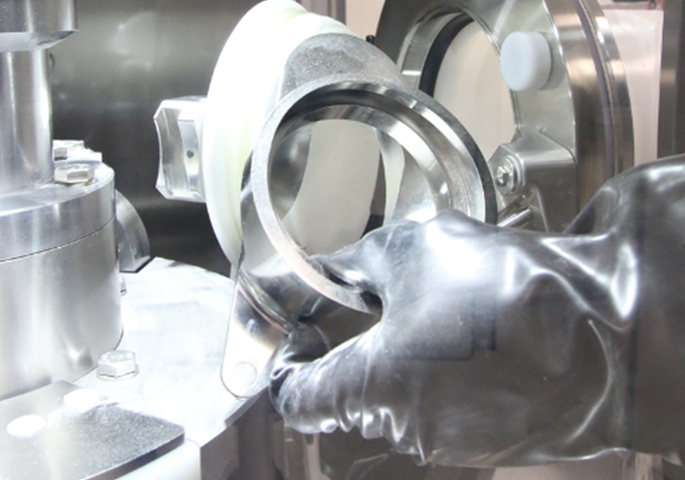
The DryCon® kit can be enhanced to permit contained intervention in the compression zone during operation by adding glove ports, a Rapid Transfer Port (RTP), and a manual dust extraction wand which is accessed via the glove ports.
Additional cleaning materials, including manual spray bottles and wipes, can be introduced to the compression zone through the RTP, which is docked on to the tablet press with a dust-tight seal. Manual pre-cleaning is performed with the windows closed and with the negative pressure control system in operation. Final cleaning at the conclusion of a batch campaign is generally performed wearing personal protective equipment (PPE).
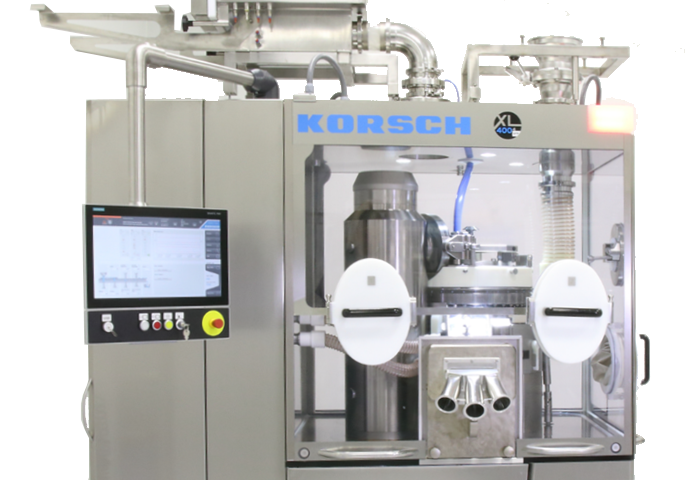
The DryCon® tablet press can work with a house dust extraction unit or a stand-alone, contained dust extraction unit - which can be provided by KORSCH.
A suitable containment valve may be adapted to the tri-clamp connection on the top of the machine if required. KORSCH can integrate the operation of the containment valve into the control system of the tablet press. KORSCH has extensive experience with the integration of all makes and models of containment valves.
The discharge chute channels on the press are configured with standard tri-clamp connections and may be equipped with continuous liners that will provide a contained solution for the transport of good tablets and the collection of reject and sample tablets.
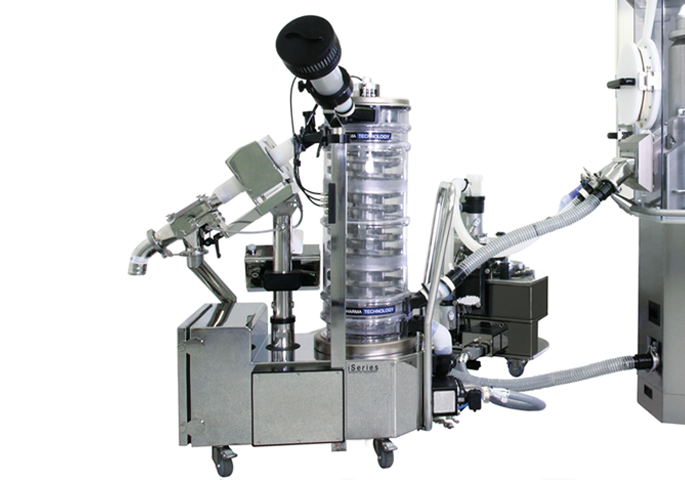
The DryCon® tablet press may be configured with a full array of related peripheral equipment, which is specified to meet the OEB 3 or OEB 4 containment requirements of the system.
WipCon® Execution
KORSCH offers a Wash-in-Place and high-containment execution (WipCon®) which permits a containment level of OEB 4 or OEB 5.
The WipCon® execution is designed and built based on two main technical requirements: dust tightness suitable for OEB 4 and OEB 5 (compression zone as an isolator with inflatable seals) and Wash-in-Place functionality with comprehensive sealing. The glove ports, RTP, and negative pressure control are included as standard in the WipCon® execution. It is important to note that PPE is not required for any aspect of the WipCon® setup, operation, or cleaning.
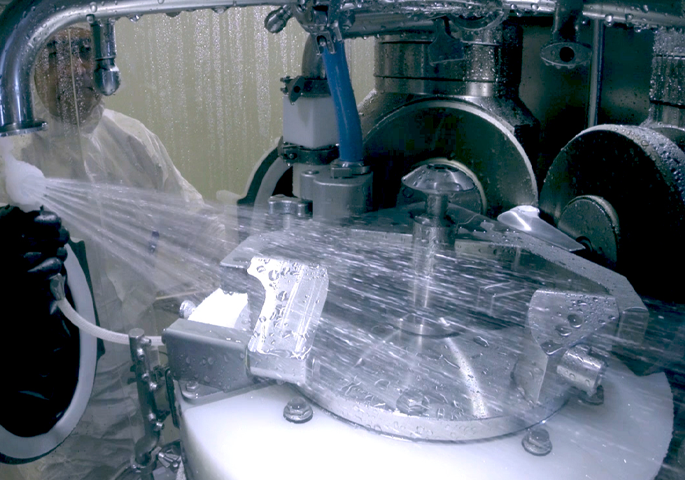
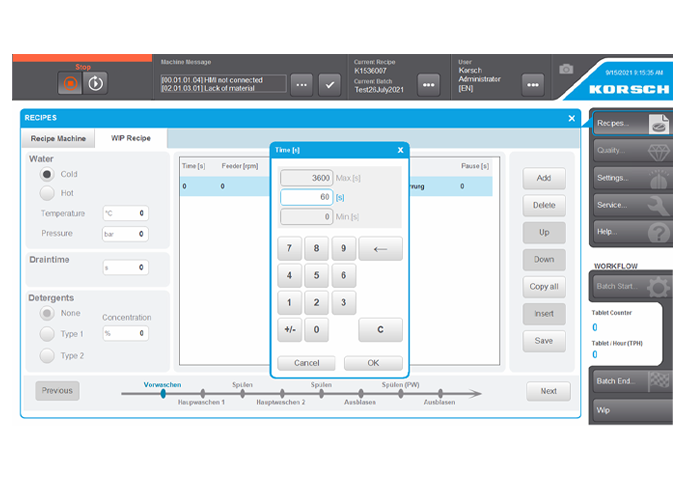
All KORSCH models configured with WipCon® technology include compression zones of certified stainless steel and special plastic materials that are suitable for washing using hot water up to 60° Celsius with acidic or alkaline detergents.
The WIP cleaning sequence begins with a prewash cycle which removes any residual powder and airborne particulate from the compression zone. The initial prewash and wetting the interior of the press makes it possible to dismantle certain components, including the compression tools, via the glove ports and RTP. This makes further cleaning easier. Depending on cleaning requirements and solubility of the active material, dismantled machine components can also be removed from the compression zone in a contained manner via an RTP prior to the full WIP sequence.
In subsequent wash cycles, all tubes are wetted completely, and a series of spray nozzles are activated in the compression zone for a preset time duration. The WIP sequence also incorporates the peripheral equipment including the deduster, metal detector, tablet tester, and air handling system. The operator can also access the inside of the machine through glove ports and manually perform supplemental cleaning using the handheld spray gun.
The final stage of the WIP cleaning sequence consists of a single or multiple rinse cycles, before the machine can be opened safely for any final cleaning and drying, without the requirement for PPE. The WIP sequence may be stored in a recipe format to permit a repeatable and validated Wash-in-Place procedure. An optional hot air dryer may be incorporated into the system design to automate the post WIP drying process.
Turnkey Engineered Solutions
For all containment applications - DryCon® or WipCon® - KORSCH provides highly specified, fully integrated solutions for the safe and efficient operation, which consist of the tablet press and all related peripherals, including the deduster / metal detector, tablet tester, inlet HEPA filter, containment valves, continuous liners, and negative pressure control system.
An advanced and fully integrated control capability provides centralized control and reporting for all system components while meeting the audit trail and data integrity requirements of
21 CFR Part 11.
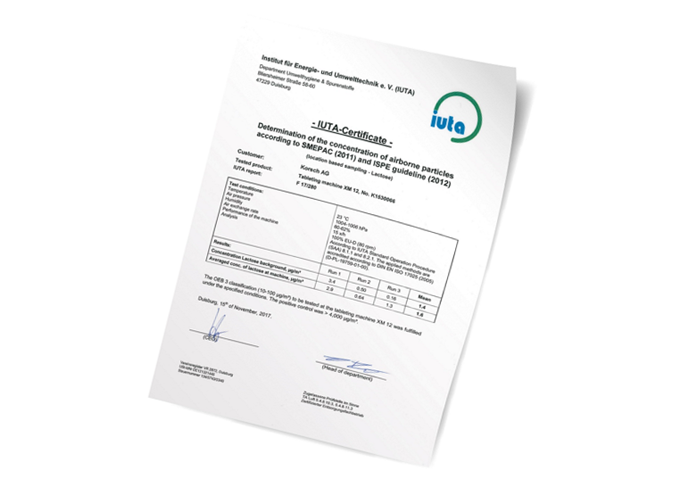
Certified Containment Capability
KORSCH has conducted comprehensive SMEPAC (Standardized Measurement of Equipment Particulate Airborne Concentration) testing on all containment machines to verify the integrity of the system design and full compliance with OEB requirements.