Systems Engineering for High Containment
Given the resulting complexity, pharmaceutical manufacturers require a fully integrated, systems engineering approach – from specification to SMEPAC testing – to ensure that the tablet press and related peripherals are fully aligned with the OEL requirement.
Localizing potential hazards
Generally speaking, the starting point for any containment consultancy is to determine the Occupations Exposure Band (OEB) for the system. This is determined based on the nature and concentration of the active ingredient. There are dramatic differences between the technical complexity and the required investment level for OEB 3 (10-100 µg/m3) capable systems, versus OEB 4 (1 – 10 µg/m3) and OEB 5 (< 1 µg/m3) systems. In general, the industry is moving away from direct on-operator PAPR (powered air purifying respirator) towards containment systems on the equipment and related peripherals. Large-scale cleaning of entire rooms, where operators only wear PAPR, is extremely expensive, as is operator decontamination.
The issue of waste management is an equally important part of the containment system engineering plan. Potent dust that has been collected in the air handling system, and contaminated waste water must be treated or disposed of properly. “That is a complex and costly process, which needs to be factored into plans for any new production facility at an early stage,” confirms Mr. Nitzsche.
KORSCH has been developing fully integrated, high-containment, wash-in-place, tablet compression systems since 1999. These systems can be highly customized to meet the most stringent specification, and are always engineered to provide the safest, and most cost-effective solution for OEB 3, OEB 4, and OEB 5 applications.
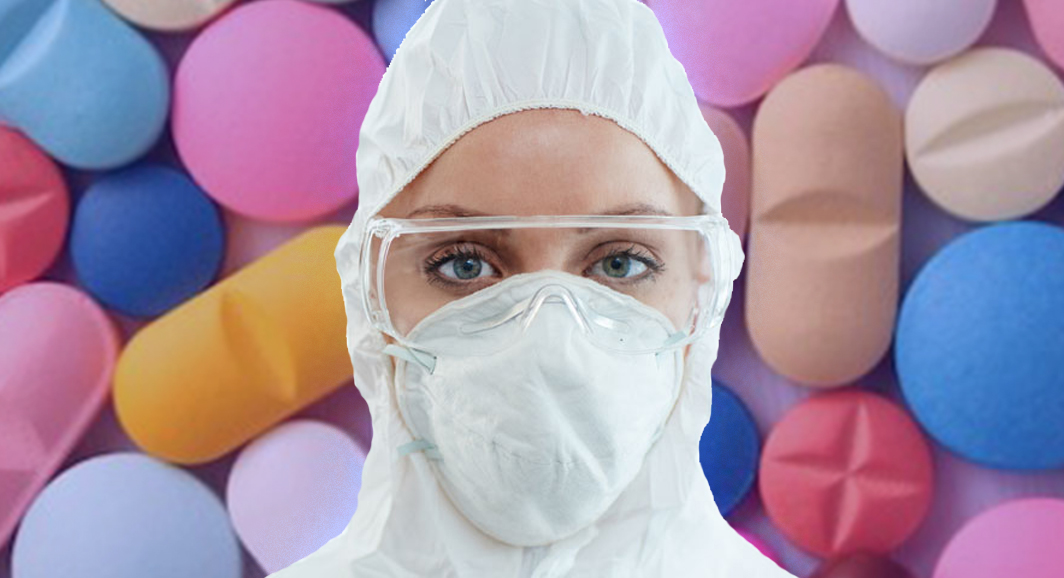