XL 800
HIGH CAPACITY
XL 800 - Double-Sided Tablet Press
The XL 800 is a reliable workhorse designed for high speed (up to 120 RPM), high volume, fully automated 24/7 operation. The machine offers an innovative bi-layer conversion kit which permits to run both single-layer and bi-layer formats on the same machine. The exchangeable turret design allows the production of any tablet size.
DOUBLE-SIDED TABLET PRESS
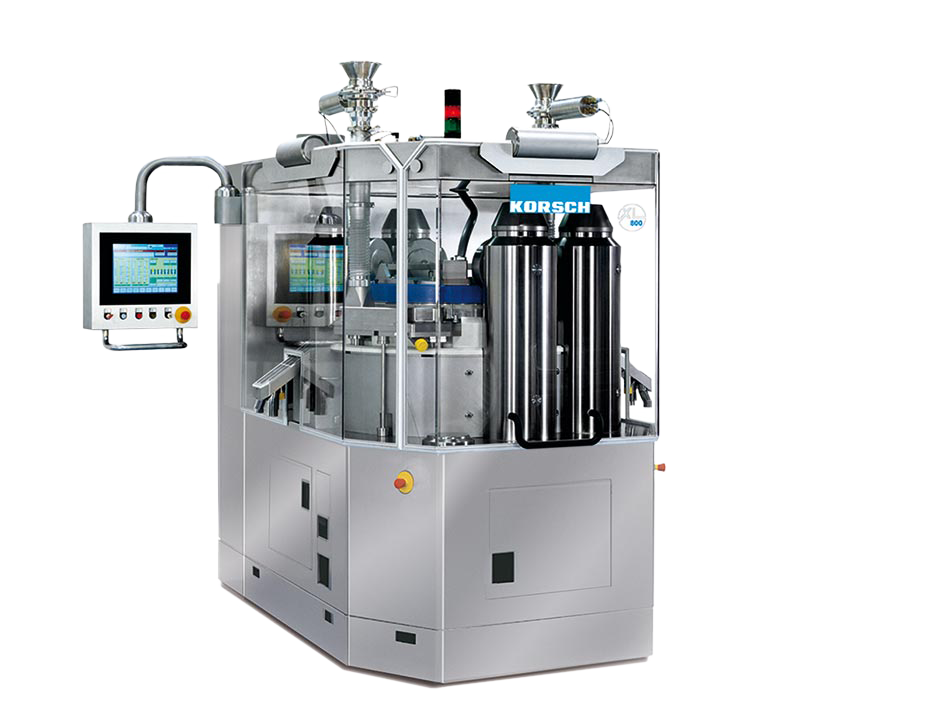
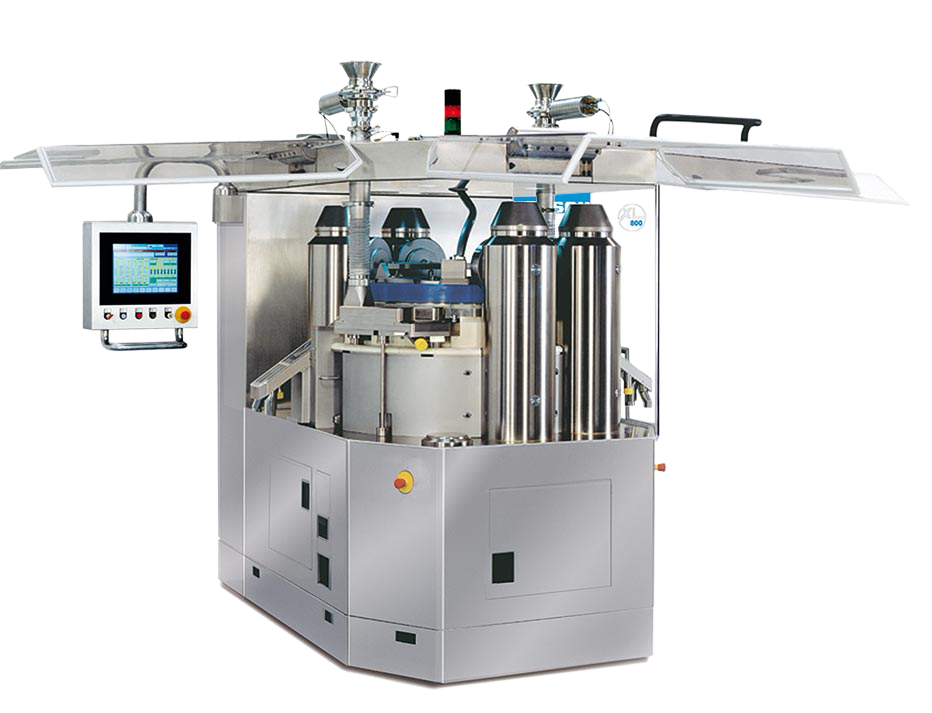
> 1 MIO single-layer Tabs/h.
Bi-Layer Capability
Turret Removal Capability
100 kN / 100 kN
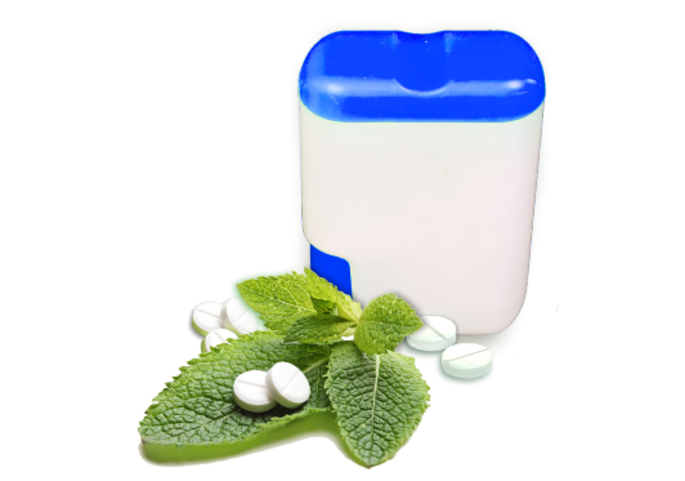
Food & Confectionary Applications
The machine complies with the highest standard in GMP- and all valid FDA-regulations. Each machine can be configured to meet specific customer needs like:
- Special shape tablets
- Ring Formats tablets(center pin)
- Chewing Gum Tablets
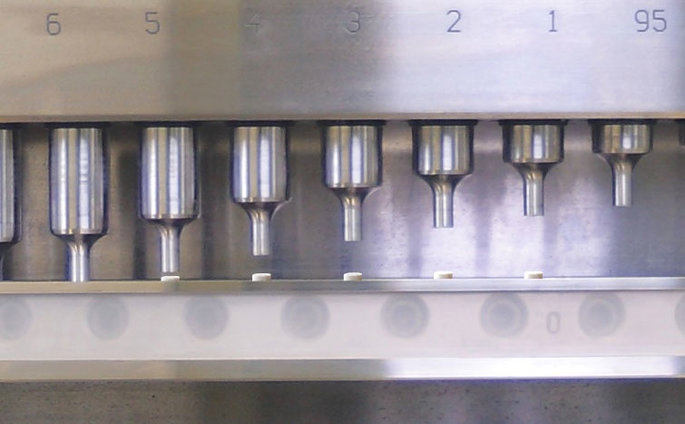
HIGH EFFICIENCY
The KORSCH expertise is the optimal utilization of the pitch circle of the tablet press, from die filling to tablet ejection. The long feeder lengths, smooth cam tracks, and the compression dwell bar all combine to permit maximum throughput without any compromise on product quality.
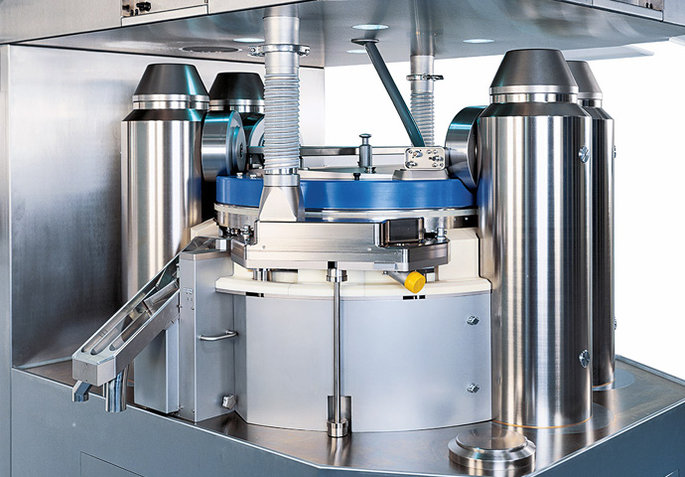
User Friendly Operation
The design concept of the XL 800, with the multi-function column at the rear of the machine, and without the need for corner columns around the compression zone, offers optimal access for set-up, cleaning, changeover, and maintenance. The Through-The-Wall installation option offers access to all major machine components from the service area.
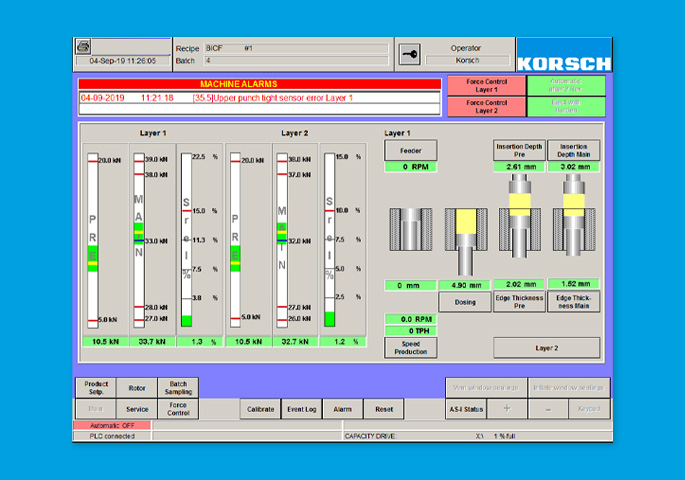
Touch Screen Control
KORSCH controls are based on a standard Siemens PLC. The touch screen HMI also uses industry standards, including WinCC, which are operating on an industrial PC platform.
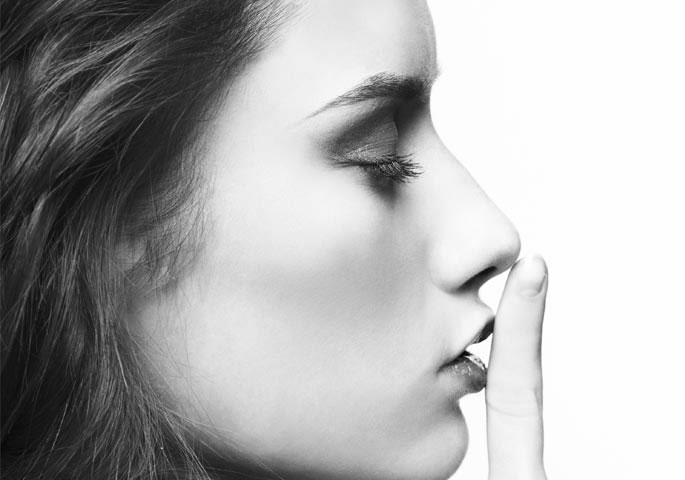
Minimal Noise and Vibration
The unique and patented design of the carrier plate, with dampers, fully isolates vibration from the head piece and machine base. The result is:
- Very low noise emission < 80 dB(A)
- No vibration transmission to the floor of the compression room
- No segregation of powder in the feeding system wich can occur with machine vibration
Containment Solutions
KORSCH offers a wide range of containment solutions on most machine models, including DryCon and WipCon® executions. With proven solutions across the full containment range (OEB 3, OEB 4, OEB 5), KORSCH provides a fully turnkey system which is engineered to meet the specific requirements of the project. In partnership with the customer, KORSCH specialists define critical process parameters, including containment requirements, peripheral integration, and automation design. KORSCH engineers are expert in developing the concept, execution, integration, and final SMEPAC testing to fully validate the containment capability.
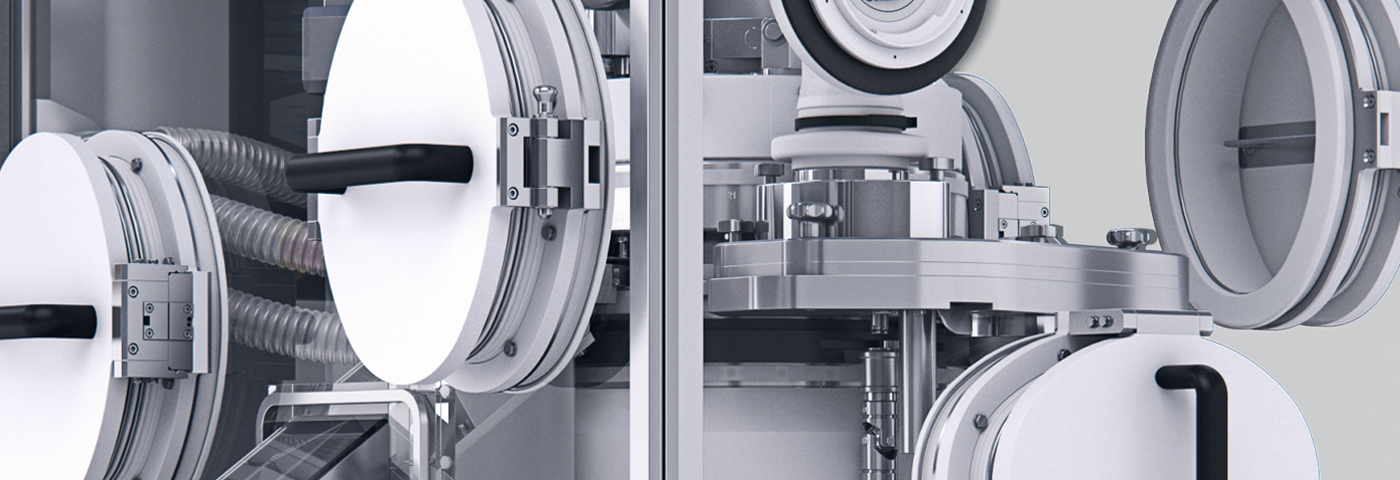
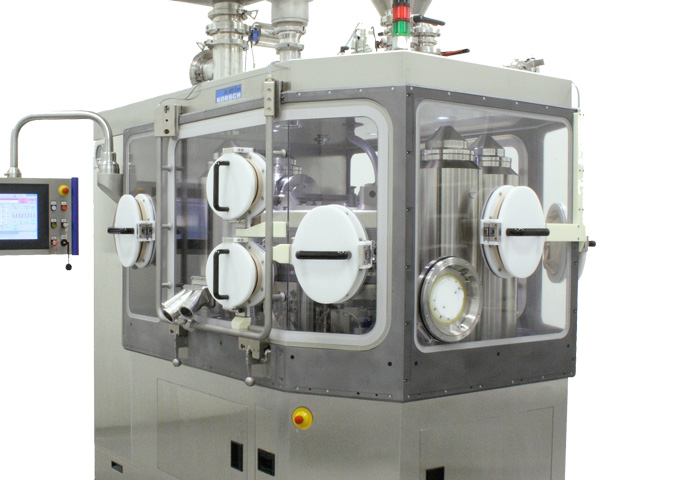
XL 800 DryCon
The XL 800 DryCon is a double-sided rotary press for high-volume manufacturing of highly active but not highly toxic ingredients. The DryCon execution permits contained access to the compression zone and eliminates the requirement for personal protection equipment (PPE) during operation.
XL 800: Downloads
Download our brochure or have a look at the technical data:
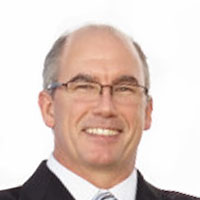
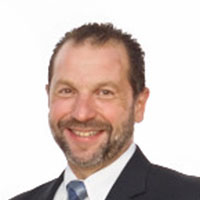
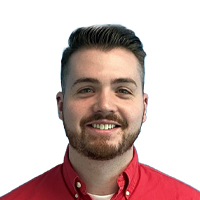
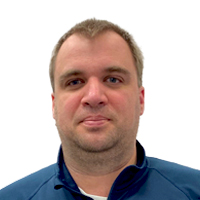