X 5
Single-Sided Maximized
The KORSCH X 5 is a new addition to the KORSCH equipment portfolio that dramatically increases single-sided tablet output while maintaining the company’s hallmark flexibility and fast change design. The machine features enhanced accessibility, ergonomics, and a compact design with an integrated control cabinet.
The advanced control system interface provides an intuitive operating environment and Smart-Touch HMI. The X 5 is smart and Pharma 4.0 ready, which permits a deeper understanding of what is happening in the compression suite.
Single-Sided
tablet press
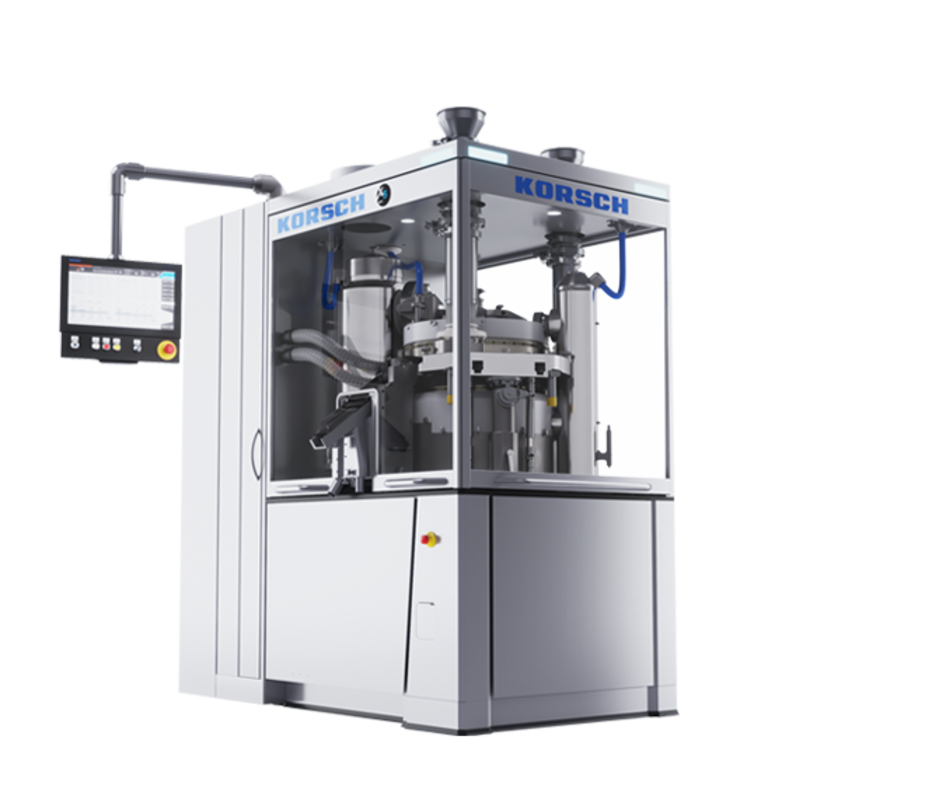
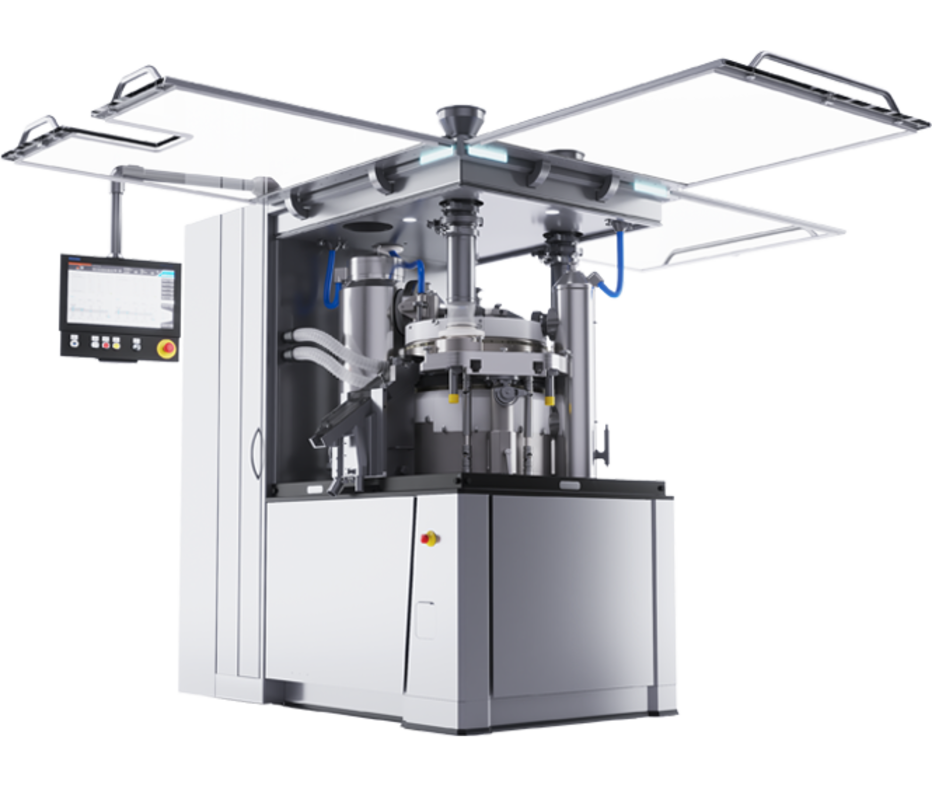
Maximized Output
Multi-Layer Capability
Smart & Pharma 4.0
Extremely Long Filling Length
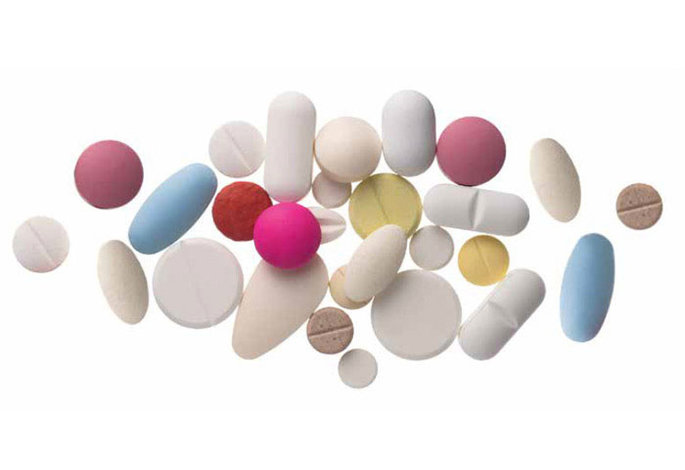
Designed for Pharma & Nutraceuticals
The X 5 complies with the highest standard in GMP- and all valid FDA-regulations. KORSCH controls permit full compliance with 21 CFR Part 11. The machine offers precision tablet weight control. Extended filling length permits superior weight uniformity. The "Through The Wall" installation option allows the true separation between production and technical area.
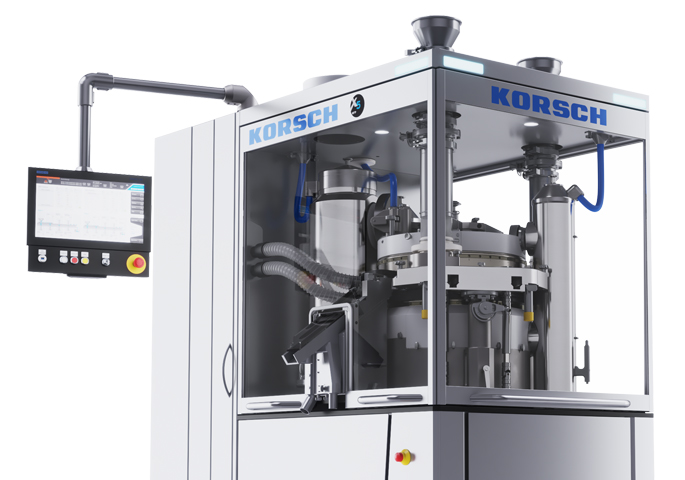
Maximized Output
With die turret design, the X 5 offers an output capability that is 20% higher than most single-sided tablet presses on the market without a significant increase in the machine footprint.
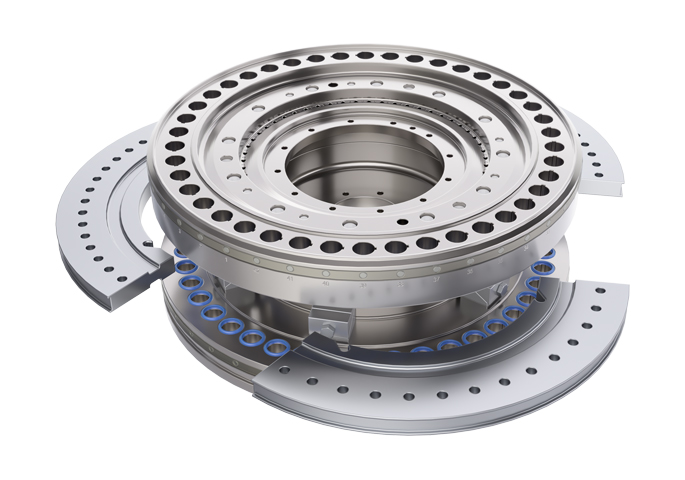
Optional Turret Design with Segments
Furthermore, the X 5 features an optional turret segment design, which uses standard upper and lower punches, and three die table segments which are configured for the size and shape of the tablet to be produced.
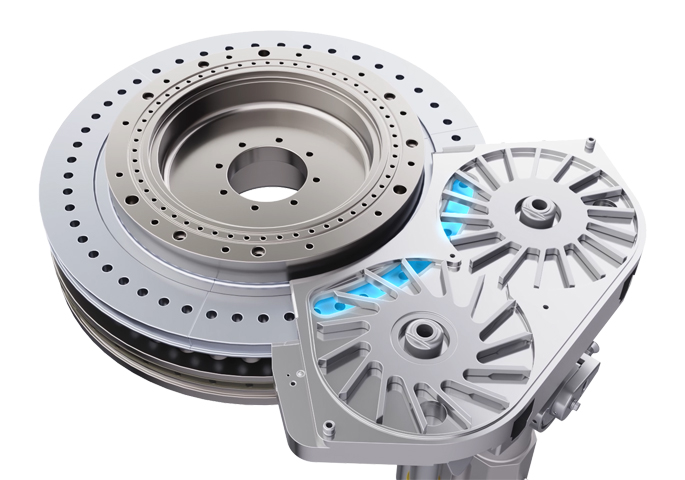
Operational Efficiency
With a powerful torque drive, a long feeder design in relation to the pitch circle, and a precision tablet weight control, the X 5 is geared for high-output manufacturing. The water-cooled chiller serves both the torque drive as well as the heat exchanger in the integrated electrical cabinet, which translates to a machine exterior that is completely sealed.
The X 5 is offered in two versions: the X 5 SFP provides dedicated single-layer capability, while the X 5 MFP combines single-layer, bi-layer, and tri-layer flexibility. Both models share a common turret and interchangeable product contact parts for maximum efficiency and flexibility in high-speed, high-volume production environments.
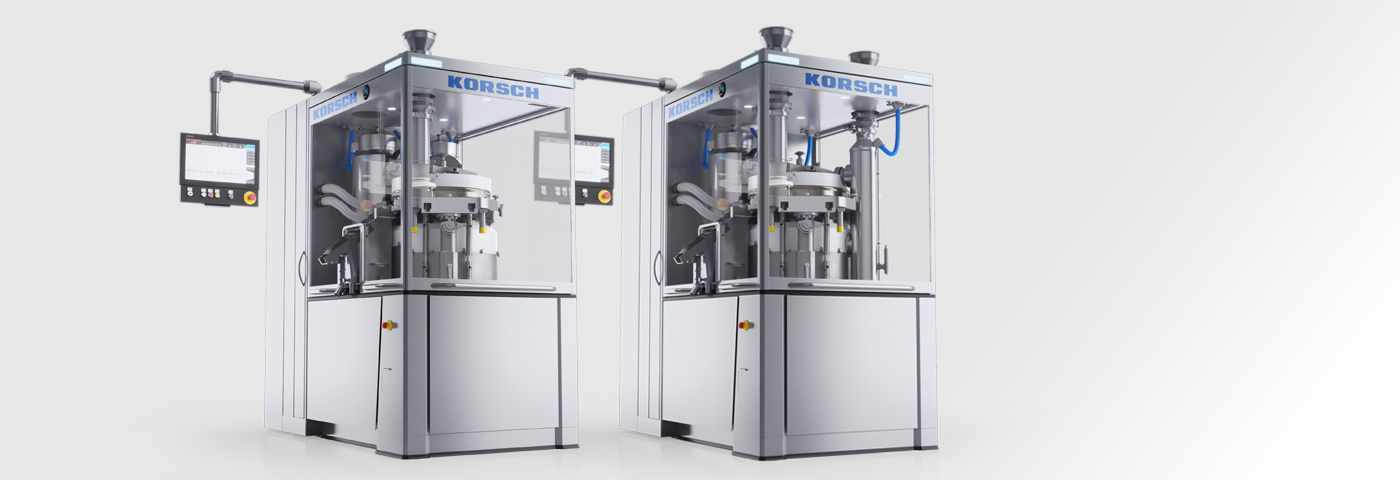
X 5 SFP
Dedicated Single-Layer High-Speed Production
- Up to 518,400 single-layer tablets per hour
- 20/100 kN precompression capability
- 100 kN main compression capability
- 120 RPM maximum press speed
X 5 MFP
Flexible Single, Bi, and Tri-layer High-Speed Production
- Up to 518,400 single-layer tablets per hour
- Up to 259,200 bi-layer tablets per hour
- Up to 216,000 tri-layer tablets per hour
- 20/100 kN precompression capability
- 100 kN main compression capability
- 120 RPM maximum press speed
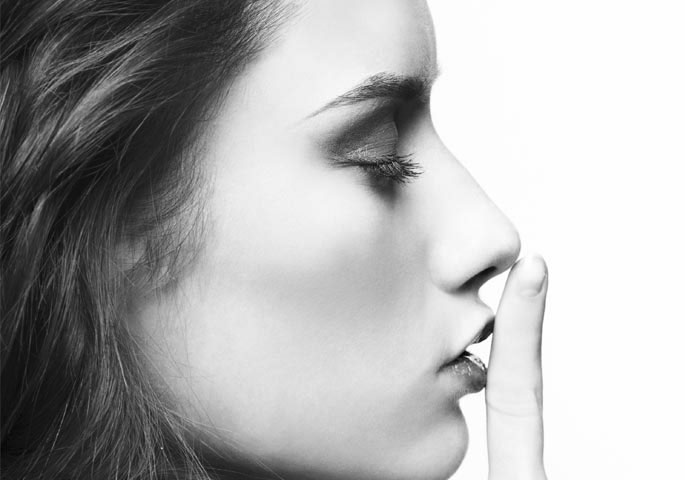
Minimal Noise and Vibration
The carrier plate that supports the dual column for pre and main compression is mounted on dampers. This unique and patented design fully isolates vibration from the head piece and machine base. The result is an extreme reduction in operating noise level.
- Very low noise emission <80 dB(A)
- No vibration transmission to the floor of the compression room
- No segregation of powder in the feeding system which can occur with machine vibration
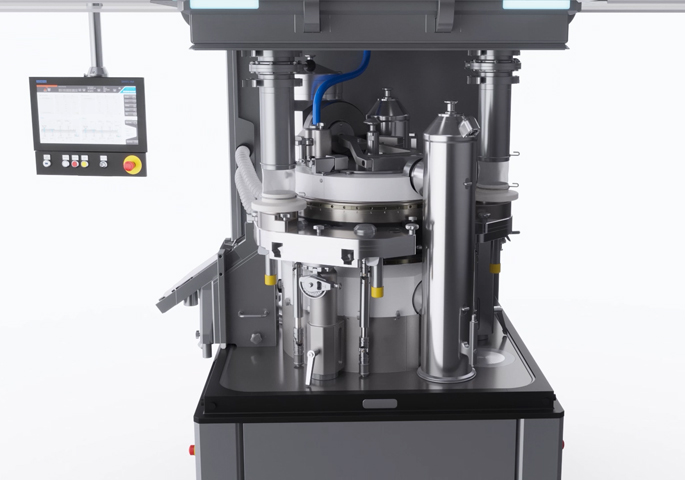
Fast and Easy Changeover
For changeovers, superior compression zone access through the lack of corner columns, smooth surfaces, and minimal fast change parts yield an expedited process for maximized machine uptime.
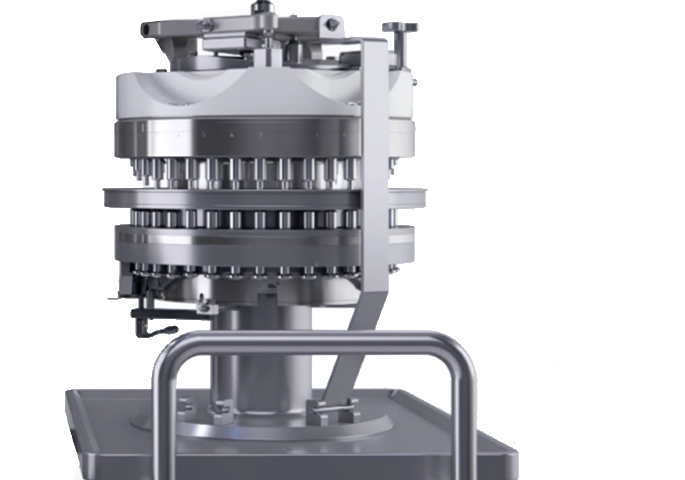
Turret Removal
The X 5 turret may be exchanged – quickly, easily, and safely – including the cams, and press tools.
- Turret removal in less than 10 minutes
- Same lifting arm permits the removal of the compression columns
- Transport cart for turret preparation and off-line cleaning
The X 5 is fully prepared to fit into the smart factory concept. The KORSCH control system features an open architecture and the ability to easily integrate the machine to a central network, with domain authentication, central recipe management, and central batch report archiving. In addition, a standard OPC UA Server permits press parameters to be passed to a SCADA or Historian system in real time. Advanced capabilities further leverage the data through Edge Computing solutions for OEE assessment and predictive maintenance. In addition, machine data may be made available for sharing with external systems through secure Cloud or VPN connection.
Programming Suitable for Industry 4.0
To reach the goal of Industry 4.0 which is a fully digital supply chain, the key point is that all components can communicate inside the machine and to external systems. The X 5 is MTP (Modul Type Package) Ready: It features a standardized interface for the integration of the machine with upstream and downstream process equipment.
- Programming of all machine components on one single platform (SIMATIC Drive Controller )
- Programming according to Norm PackML (Packaging Machine Language) from OMAC
- Tableting control algorithms based on our Specialists’ knowledge are constantly optimized
Intelligent Components Industry 4.0 Ready
In order to support required advances in operational efficiency, the X 5 is smarter. This means that the machine features intelligent sensors which play a key role in making Industry 4.0 a reality. Sensors which function on a fully digital basis enable data to be interpreted accurately for process monitoring and control.
- Smart sensors, featuring IO link, to pre-process data
- Memorizing sensor technology enables machine to be stored directly in the sensor
- Electronic type plates record identity, configuration, and calibration of components
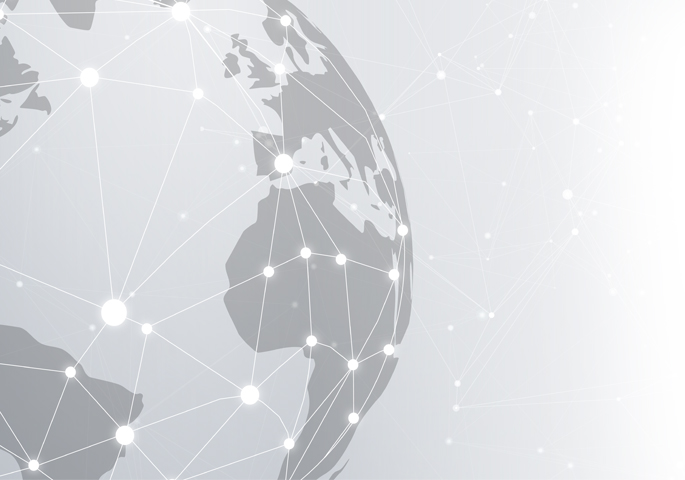
Edge and Cloud Solutions
Digitalization of the machine permits data to be transmitted to an Edge device or a secure cloud solution. Edge or Cloud computing can analyze and process these data via different apps and software. Data can also be made available for external service providers, if required.
- Calculate and visualize key performance indicators to detect optimization potential
- Calculate and assess OEE and efficiency optimization strategies
- Track and optimize energy consumption of your machine
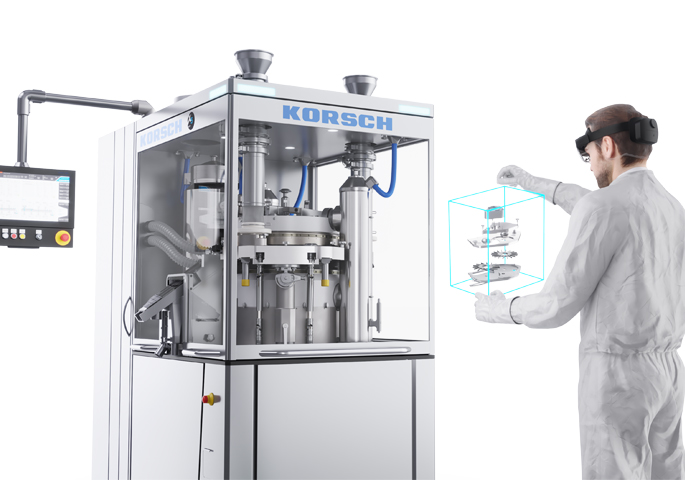
Augmented Reality Support with PHARMAVIEW®
Operator training, on an augmented reality or virtual reality platform, will reinforce best practices and raise the competency level.
- Holographic Support for production, trouble shooting and maintenance
- Access to Multi-media Support Files
- Augmented Training (without machine or on the machine to see inside the assemblies)
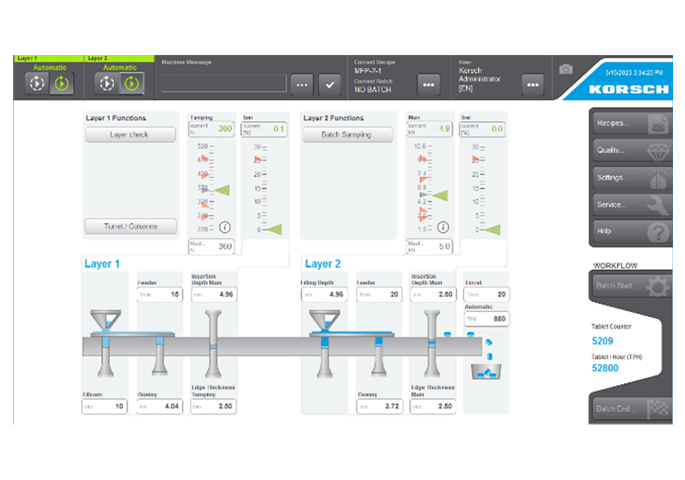
Intuitive Controls with Smart-Touch HMI
The advanced control system interface provides an intuitive operating environment and Smart-Touch HMI. The HMI environment offers a comprehensive On-Board help capability, which includes a vast array of multi-media help files to present procedures and to support the operation and maintenance of the machine. At the heart of the control system is a Siemens Simatic Drive Controller, which merges PLC and motion controls in a single, integrated system. This permits extensive remote diagnostic support.
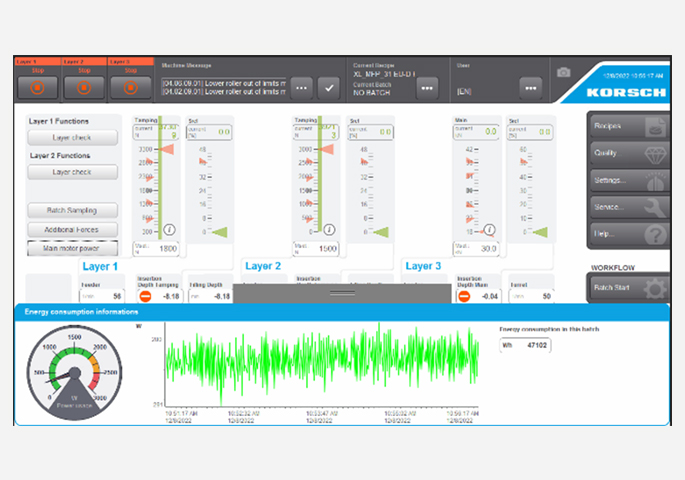
Energy Consumption
Real-time display of the energy consumption: Monitoring and display of energy consumption to support sustainability initiatives at site level.
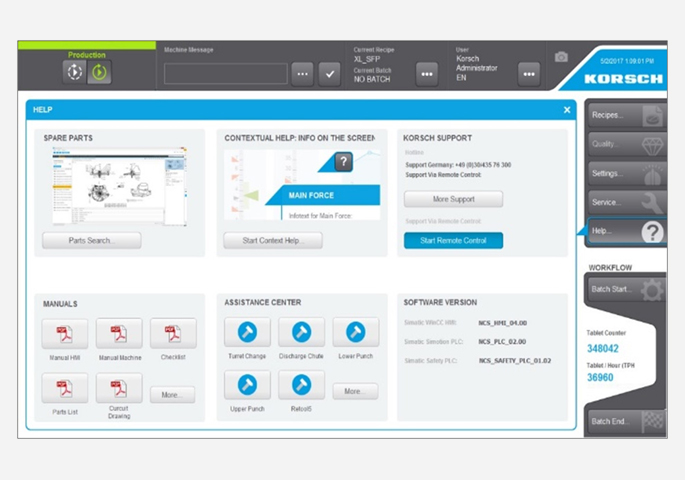
On-Board Help Capability
The Smart-Touch HMI sets a new standard for help content which is integrated in the HMI environment to permit direct access during the machine operation and maintenance.
- Direct link to support documents, including manuals, drawings, and schematics
- Multi-media support files (videos, pictures) to support equipment procedures (turret change, machine changeover, calibration, etc.)
- Access to an electronic spare parts catalog
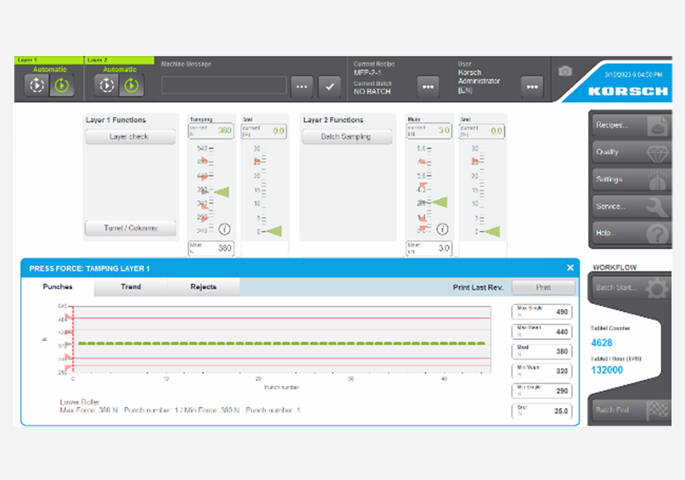
PharmaControl® Press Force System
The X 5 uses the proven PharmaControl® press force control system to monitor individual compression forces and to provide closed loop feedback to the dosing cam for precise tablet weight control. The optional single-tablet rejection system will reliably reject an individual tablet from a known punch station across the full speed range.
KORSCH offers a wide range of containment solutions on most machine models, including DryCon and WipCon® executions. With proven solutions across the full containment range (OEB 3, OEB 4, OEB 5), KORSCH provides a fully turnkey system which is engineered to meet the specific requirements of the project. In partnership with the customer, KORSCH specialists define critical process parameters, including containment requirements, peripheral integration, and automation design. KORSCH engineers are expert in developing the concept, execution, integration, and final SMEPAC testing to fully validate the containment capability.

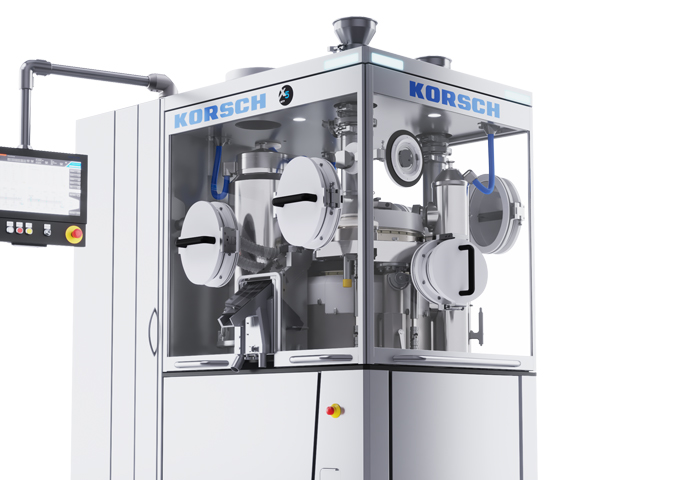
X 5 DryCon
The X 5 is offered in a dry containment execution (DryCon) for OEB 3 and OEB 4 applications. For all containment projects, KORSCH provides a fully integrated and turnkey system, including support documentation and SMEPAC testing.
- OEB 3/4 containment capability
- Ergonomic placement of glove ports and RTP permit contained access to the compression zone
- Negative pressure control and integrated vacuum wand for dry cleaning
- Eliminates requirements for PPE
- Formal SMEPAC Testing for containment level certification